
Quality Control
You are reading about QUALITY | Skip to TECHNOLOGY >
An ever present commitment
A culture of quality and the pursuit of excellence are the threads that weave the fabric of Lafitte Group’s global activities. All stages of production, from selection of raw materials to quality assurance of outgoing orders, are submitted to an integrated monitoring and verification system.
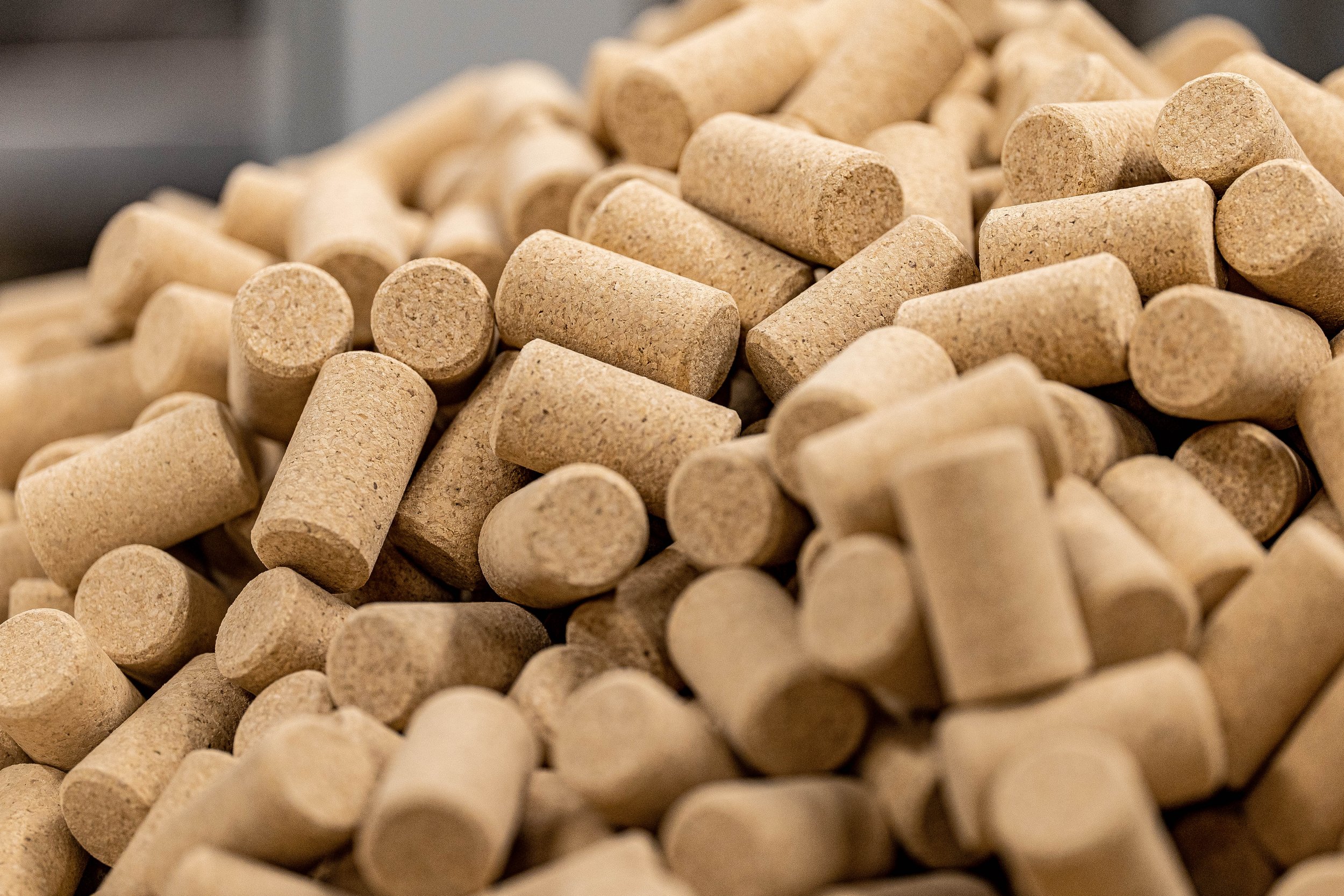
+8,000
TCA analysis (per year)
+4,000,000
Cork stoppers analyzed with PerfectGO (per year)
+6,000,000
Sensory-tested corks (per year)
Quality control.
Few companies are as focused and driven as Lafitte. A commitment to innovation and quality is paired with generational know-how to design processes and equipment that allow us to guarantee faultless products.
The raw material goes through several levels of control during production. Our demanding quality standards are measured at each phase of production by operators using advanced testing and measurement techniques. It is further inspected by the lab to guarantee the pre-established quality standards.
Our quality control
-
Preventive Processes
Creating a perfect product takes dedication from the very start. These processes ensure the right preservation of the raw material.
-
Sterilization Processes
In order to guarantee the perfect preservation of our clients’ products, we carry out a series of deep cleaning procedures to remove all unwanted odors.
-
Processes Control
Aiming for perfection is an ambitious task, but that does not faze Lafitte. We want to deliver the best possible product, and that implies controlling our own controls.
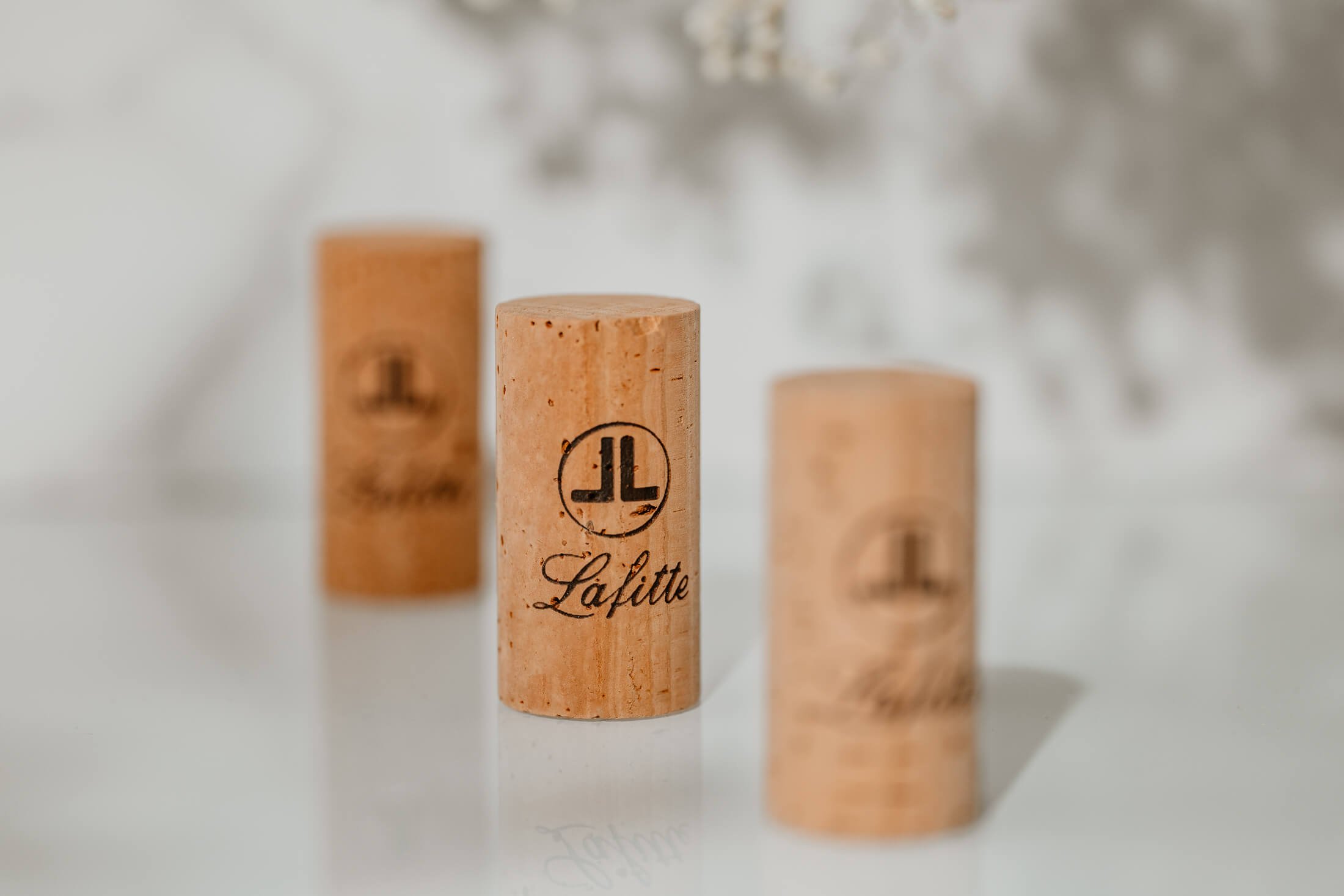
Preventive Processes.
Every effort is made to identify the most effective methodology for achieving organoleptic neutrality.
— A clean cork preparation process, with the minor impact possible to the material, respecting the safety of the workers and the environment;
— A process that selectively eliminates and extracts, with the best effectiveness possible, the unwanted organic compounds: chlorophenols and chloroanisoles;
— A process that does not affects the other organic compounds of the cork, responsible for the indispensable properties of the cork as raw material for bottle sealing and wine preservation.
Optimal storage of the cork planks
Cork planks are placed in a patio for a minimum stabilization period of 6 months, until they obtain a uniform moisture content. Cork piles are identified to allow the batches to be traced back to their origin.
Traceability is an essential point to certify the management system by the International Code of Good Practice and the Chain of Custody.
Cork piles are constructed in a rectangular shape, perpendicular to the prevailing wind and on top of cement beams, to maximize air circulation, facilitate water drainage and prevent microbial contamination.
Boiling cork
Cork planks are boiled in stainless steel tanks, to remove impurities, clean the entire surface and allow the cork to reach the ideal moisture content for processing. Each batch is boiled for one hour, reaching 20% more volume at the end, making them more regular and easier to work with.
Cork selection
After the resting period, planks are chosen by specialized operators to be transformed into natural corks. The thinner planks will be used to manufacture discs for technical stoppers.
Autoclave
Process of deodorization, dimensional and hygrometric stabilization of prepared cork planks, by the combined action of water steam, pressure and temperature, under optimized conditions.
Sterilization Processes.
MaxClean
At this stage, the granules undergo a complementary treatment to extract volatile organic compounds (such as 2,4,6 - TCA) and reduce the microbiological load by steam drag.
MaxClean Evolution (for cork stoppers)
Employed in the treatment of natural corks, this technology provides non-detectable TCA cork stoppers. Compounds like 2,4,6 - TCA and other undesirable organic compounds, present in the cork, are extracted by a deodorization/sterilization system through a combination of steam pressure, temperature and time, keeping intact the remarkable characteristics of the natural cork and its incomparable performance, essential for the conservation and evolution of the wines.
Processes Control.
TCA analysis
Throughout the entire production process, representative samples of each batch are subjected to chloroanisole quantification and analysis, using solid phase micro extraction (SPME) by gas chromatography - mass spectrometry (GC/MS) to detect unwanted components.
PerfectGO
PerfectGO is a unique detection system, sensitive to TCA, which segregates cork stoppers according to the level of TCA detected.
The cork stoppers are introduced into a closed and inert space and subjected to a controlled temperature, to volatilize the TCA molecule contained in the cork.
Quantification of TCA is carried out by equivalence, through solid phase microextraction (SPME) and gas chromatography - mass spectrometry (GC/MS) and allow the segregation of cork stoppers with a TCA content below the established limits, thus obtaining 100% TCA free lots.
Sensorial analysis
Cork batches are subjected to sensory analysis by specialized technicians, to control the undesirable volatile compounds in corks, particularly 2,4,6-trichloroanisol (TCA).
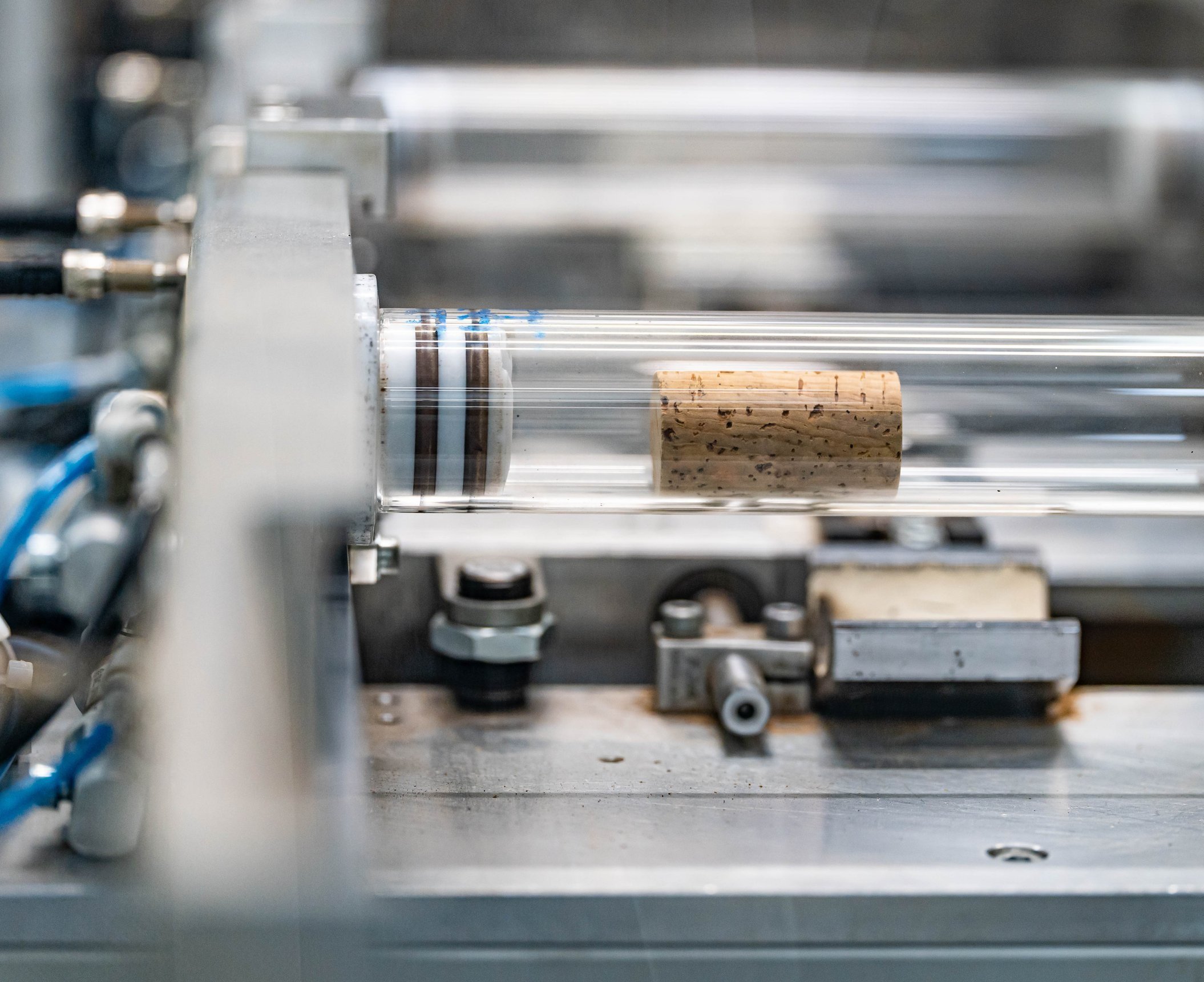
The tests performed during production can be grouped as follows:
Physical tests
Humidity
Dimensions
Density
Chemical tests
Oxidant residues
Solid residues
Sensory analysis
Chloroanisole analysis
(TCA, TeCA, PCA)
Mechanical tests
Extraction force
Sealing behavior
Capillarity
Resistance to boiling water
Elastic recovery
Others
Microbiology
Hydrostatic pump
Absorption

Quality Regulations.
We are one of the founding members of the Cork Quality Council (CQC) in California, and members of CTCOR. All material used in manufacturing and treatment is FDA approved.
Our Integral Quality Control Lab is committed to using the latest technological advancements to ensure the improvement of the production process.
In addition to our sensory analysis of all lots of cork stoppers, an external laboratory screens for TCA through SPME and GC/MS analysis to help us maximize the neutrality of all our products.
Our Napa facility operates the first ozone-infused moisture room in California. This innovative ozone generator helps to eliminate microbiological growth on treated corks without byproducts or residual contaminants.
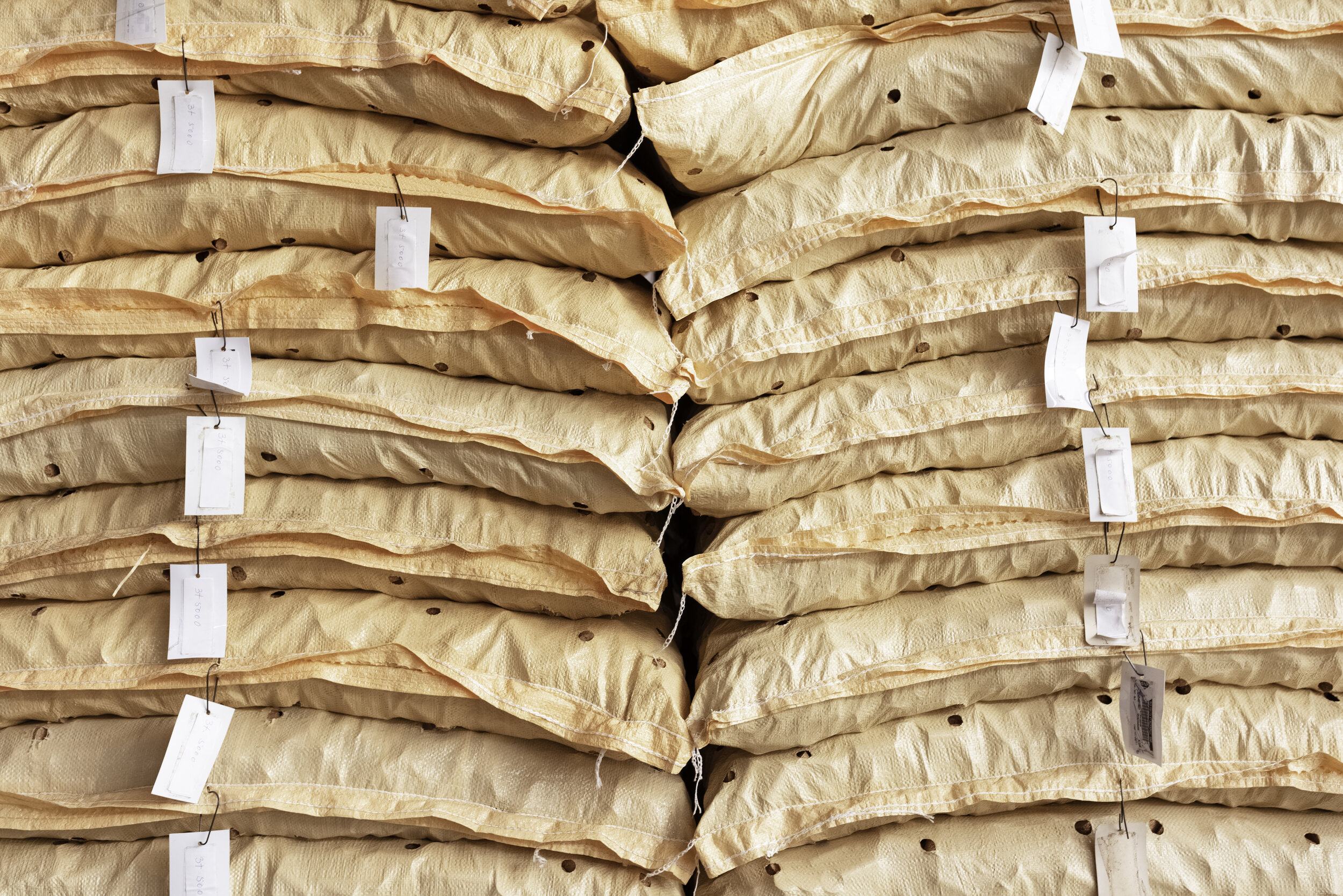
Water-Based Paint.
Our exclusive use of water-based paint for all of our capsules is an important step in delivering total quality and safety to our customers. Water-based paint offers many benefits:
Environmental Safety
Less than 5% Volatile Organic Compounds (V.O.C) and does not contain any heavy metals.
Human Safety
Non-toxic and virtually harmless, containing no CMR classified substances found in other paints, which have been linked to cancerous and teratogenic effects.
Technical Quality
The non-stick quality of this paint performs better on the bottling line for remarkable consistency.
Aesthetic Quality
Smoother, more homogenous coverage on both tin and aluminum materials.
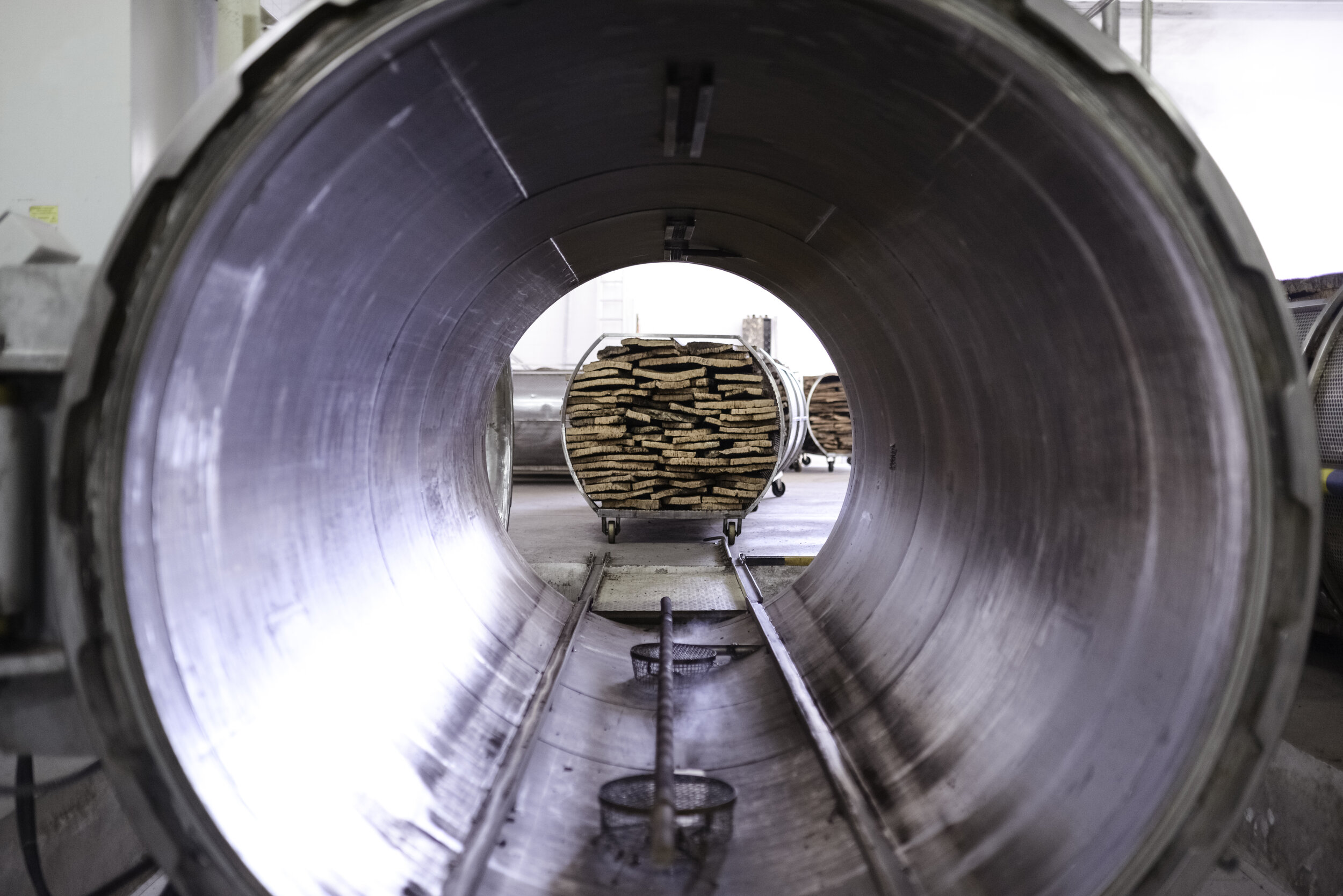
Incoming.
All incoming cork is strictly tested by Lafitte California’s quality assurance procedures and graded in accordance with Cork Quality Control (CQC) guidelines to ensure quality received complies with quality ordered.
Lafitte California subjects all incoming cork to visual and olfactory inspection, while individual lots are sampled and undergo chemical analysis.
During sampling procedures, an Incoming Quality Control Report records grade, moisture level, dimension, visual quality, residual oxidants, hygiene control, potential degradation, density, sensory effect on wine, and external TCA analysis.
Lots are stored for processing and final surface treatment by Lafitte California upon purchase order.
Processing.
Bales of punched and washed cork are stored for processing in a clean, dry, well-ventilated warehouse arranged by size and grade.
Cork is branded by request with text or a logotype to allow you to personalize the product and ensure its traceability. Daily visual inspection ensures correct color and quality of branding.
Our innovative Moisture Room, combines the newest ozone technology for moisturizing and preventing microbiological contamination to ensure cork moisture remains at an optimal 5-6%, as recommended by the CQC, to ensure a proper seal when bottling
Outgoing.
Final surface treatment of the corks is determined by the type of wine and bottling equipment used by the customer. To determine the quality of the final treatment, samples are inspected for dust levels, sealing behaviour, force of extraction, and absorption.
All results are recorded in an Outgoing Quality Control Report prior to bagging and shipping to ensure quality standards match customer requirements.
Treated and tested corks are packaged to preserve cork in ideal condition by injecting the packed bags with SO2 prior to sealing.
Routinely, cork samples are aseptically removed after packaging and sent to an outside laboratory for analysis to ensure no bacteria, yeast, or mold contamination is present.
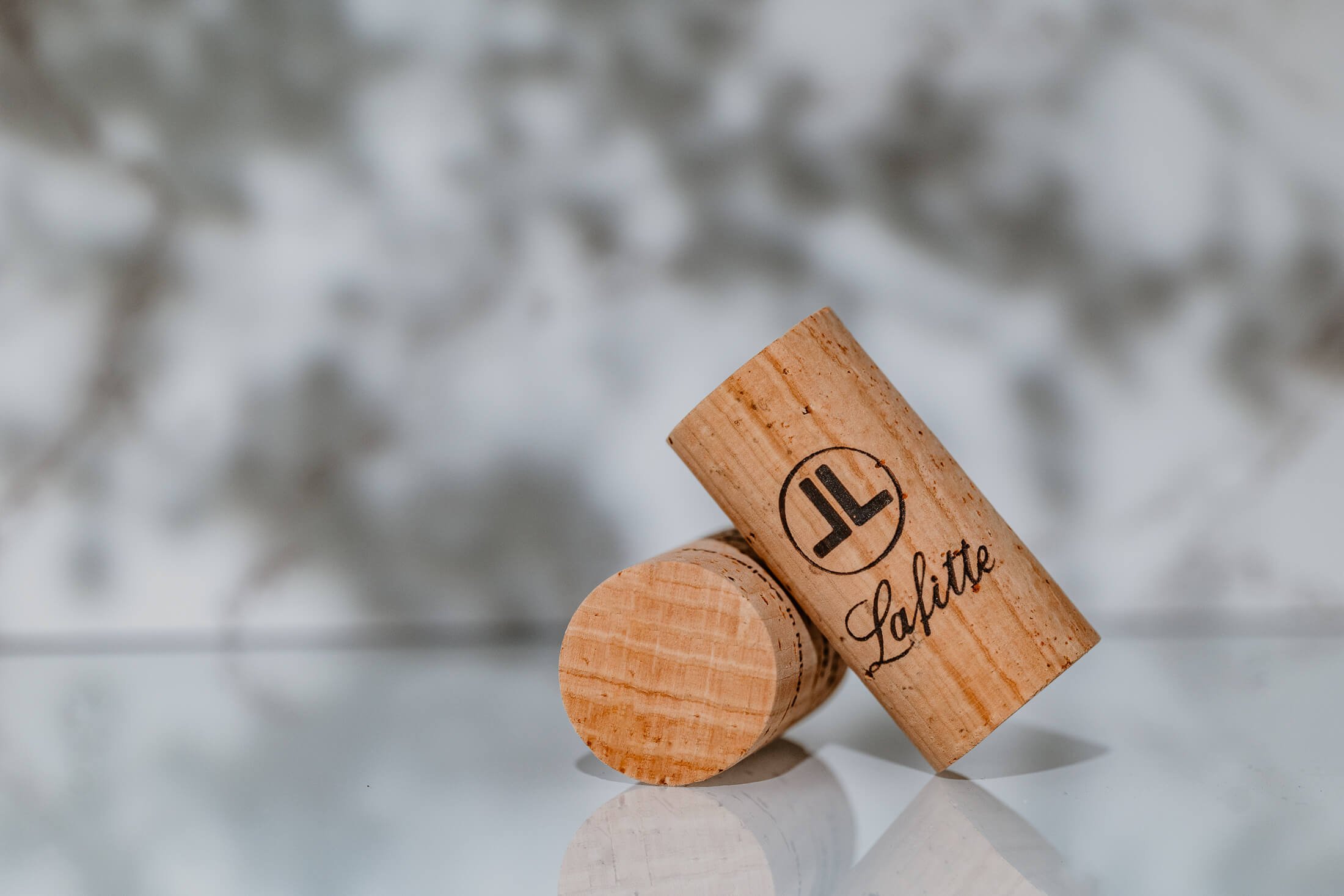